Qualitätsmanagement ist entscheidend für den Erfolg eines Unternehmens. Um Prozesse zu optimieren, Fehler zu reduzieren und Kundenerwartungen zu erfüllen, setzen Unternehmen verschiedene Methoden ein. Doch welche Qualitätsmethoden sind die verbreitetsten und wie funktionieren sie? In diesem Artikel stellen wir die meistgenutzten Methoden vor, erklären deren Anwendungsbereiche und zeigen, wo ihre Grenzen liegen.
1. PDCA-Zyklus – Der Klassiker für kontinuierliche Verbesserung

(Plan – Do – Check – Act)
Der PDCA-Zyklus, auch Deming-Kreis genannt, ist eine bewährte Methode zur kontinuierlichen Verbesserung von Prozessen. Er basiert auf einem wiederholbaren Vier-Schritte-Prozess, mit dem Unternehmen ihre Abläufe optimieren und systematisch anpassen können. Im ersten Schritt (Plan) wird das Problem analysiert und eine Lösung erarbeitet. Anschließend erfolgt die Umsetzung (Do) in einem kleinen Rahmen, um mögliche Risiken zu minimieren. In der Prüfphase (Check) wird überprüft, ob die Maßnahme erfolgreich war, bevor sie in der letzten Phase (Act) dauerhaft in den Prozess integriert wird.
So funktioniert PDCA:
- Plan (Planen): Problem identifizieren, Ziele setzen, Maßnahmen planen.
- Do (Umsetzen): Maßnahmen im kleinen Rahmen testen.
- Check (Überprüfen): Ergebnisse analysieren und mit den Zielen vergleichen.
- Act (Handeln): Erfolgreiche Maßnahmen dauerhaft in Prozesse integrieren.
Einsatzgebiete:
✔ Kontinuierliche Prozessverbesserung
✔ Problemlösung in Unternehmen
✔ Qualitätsmanagementsysteme (z. B. ISO 9001)
✔ Einführung neuer Prozesse
Grenzen:
✘ Braucht eine konsequente Anwendung, um langfristig Wirkung zu zeigen
✘ Ohne regelmäßige Kontrolle bleiben Maßnahmen oft wirkungslos
✘ Funktioniert weniger gut bei schnellen, kurzfristigen Maßnahmen, die sofortige Ergebnisse erfordern
Warum wird PDCA genutzt?
- Fördert eine systematische Optimierung von Abläufen.
- Einfach anzuwenden, universell einsetzbar.
2. FMEA – Fehler frühzeitig erkennen
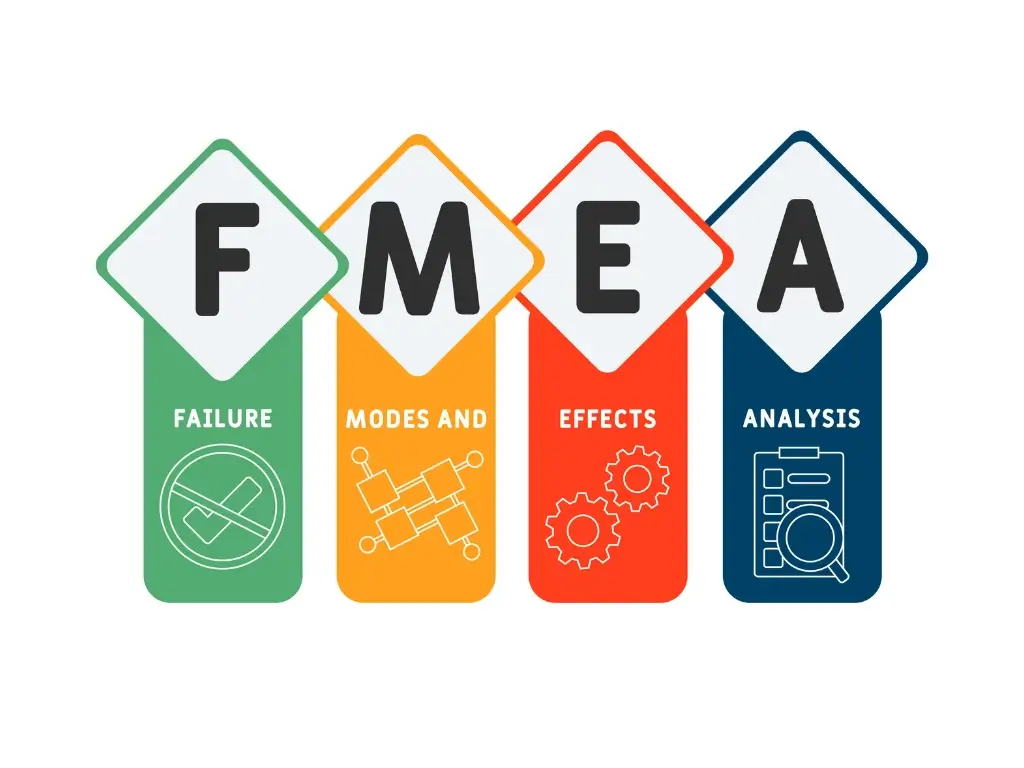
(Fehlermöglichkeits- und Einflussanalyse)
Die FMEA-Methode ist eine präventive Technik, die darauf abzielt, potenzielle Fehler in Produkten oder Prozessen frühzeitig zu identifizieren. Sie bewertet systematisch Fehlerquellen und bestimmt deren Auswirkungen auf den Gesamtprozess. Die Risikoanalyse erfolgt anhand der Risikoprioritätszahl (RPZ), die sich aus der Fehlerwahrscheinlichkeit, der Bedeutung und der Entdeckbarkeit eines Fehlers zusammensetzt. Durch die gezielte Reduzierung dieser Risiken können Unternehmen proaktiv Fehler vermeiden, anstatt sie im Nachhinein zu korrigieren. Besonders in sicherheitskritischen Bereichen wie der Automobilindustrie, Luftfahrt oder Medizintechnik ist FMEA ein unverzichtbares Werkzeug.
So funktioniert FMEA:
- Mögliche Fehlerquellen identifizieren.
- Auswirkungen und Ursachen bewerten.
- Risikoprioritätszahl (RPZ) berechnen: Wahrscheinlichkeit x Bedeutung x Entdeckbarkeit.
- Maßnahmen ableiten, um Risiken zu reduzieren.
Einsatzgebiete:
✔ Entwicklung neuer Produkte oder Prozesse
✔ Risikomanagement in Produktion und Lieferkette
✔ Qualitätsvorausplanung (APQP) in der Automobilindustrie
✔ Medizin- und Luftfahrttechnik zur Fehlervermeidung
Grenzen:
✘ Kann sehr zeitaufwendig sein, besonders bei komplexen Produkten
✘ Erfordert Erfahrung, um realistische Risiken richtig zu bewerten
✘ Falsch priorisierte Risiken können zu ineffektiven Maßnahmen führen
Warum wird FMEA genutzt?
- Reduziert Kosten durch präventive Fehlervermeidung.
- Erhöht die Prozesssicherheit und Produktqualität.
3. Six Sigma – Qualität durch datenbasierte Entscheidungen
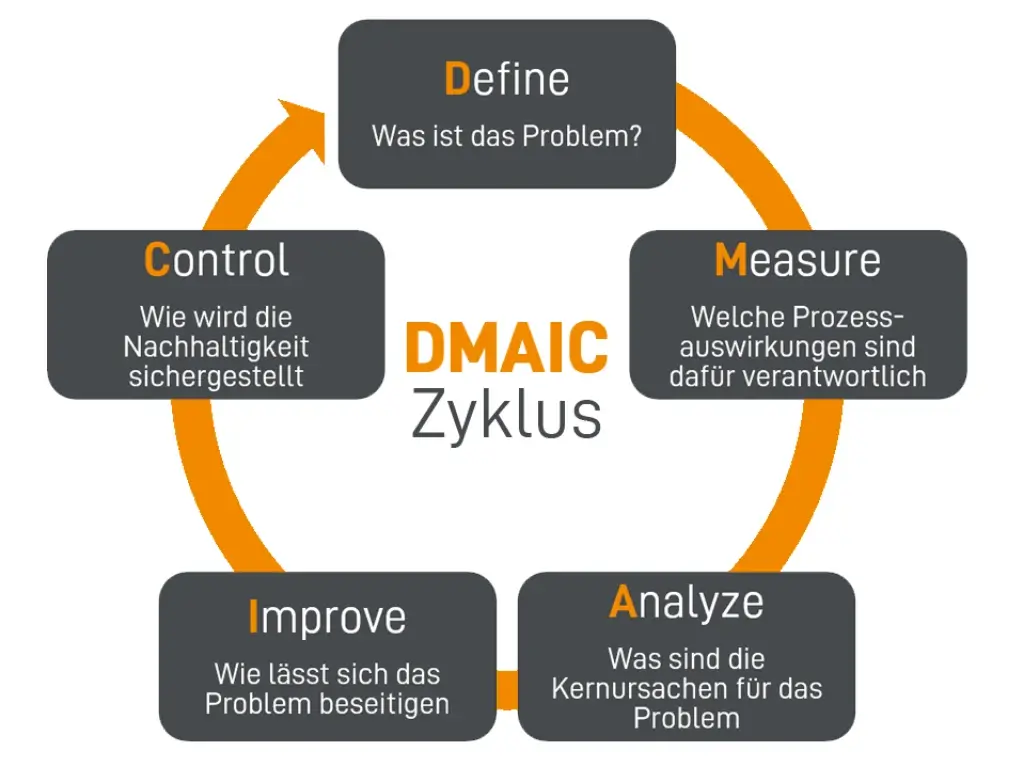
Six Sigma ist eine statistikbasierte Methode, die darauf abzielt, Prozesse möglichst fehlerfrei zu gestalten. Der Ansatz basiert auf der DMAIC-Methode (Define, Measure, Analyze, Improve, Control) und nutzt mathematische Analysen, um Abweichungen in Prozessen zu erkennen. Unternehmen, die Six Sigma anwenden, konzentrieren sich auf die Reduktion von Streuungen und Ineffizienzen, was langfristig Kosten spart und die Qualität verbessert. Durch die datengestützte Analyse lassen sich Prozesse so optimieren, dass Fehlerquoten drastisch gesenkt werden. Unternehmen wie General Electric oder Motorola haben Six Sigma erfolgreich eingesetzt, um ihre Produktions- und Geschäftsprozesse zu verbessern.
Die 5 Schritte von Six Sigma (DMAIC-Methode):
- Define: Problem und Ziele definieren.
- Measure: Daten erfassen und Prozessleistung messen.
- Analyze: Ursachen für Abweichungen identifizieren.
- Improve: Lösungen entwickeln und umsetzen.
- Control: Nachhaltige Überwachung der Verbesserungen.
Einsatzgebiete:
✔ Reduktion von Prozessvariationen und Fehlern
✔ Qualitätssteigerung in der Produktion
✔ Optimierung von Geschäftsprozessen (z. B. Finanzwesen, Logistik)
✔ Analyse von großen Datenmengen zur Effizienzsteigerung
Grenzen:
✘ Erfordert eine datengetriebene Unternehmenskultur
✘ Komplexe Implementierung und oft lange Projektdauer
✘ Nicht immer anwendbar für kreative oder agile Prozesse
Warum wird Six Sigma genutzt?
- Reduziert Prozessfehler auf ein Minimum.
- Spart Kosten durch effiziente Prozesse.
4. Ishikawa-Diagramm – Ursachen für Probleme finden
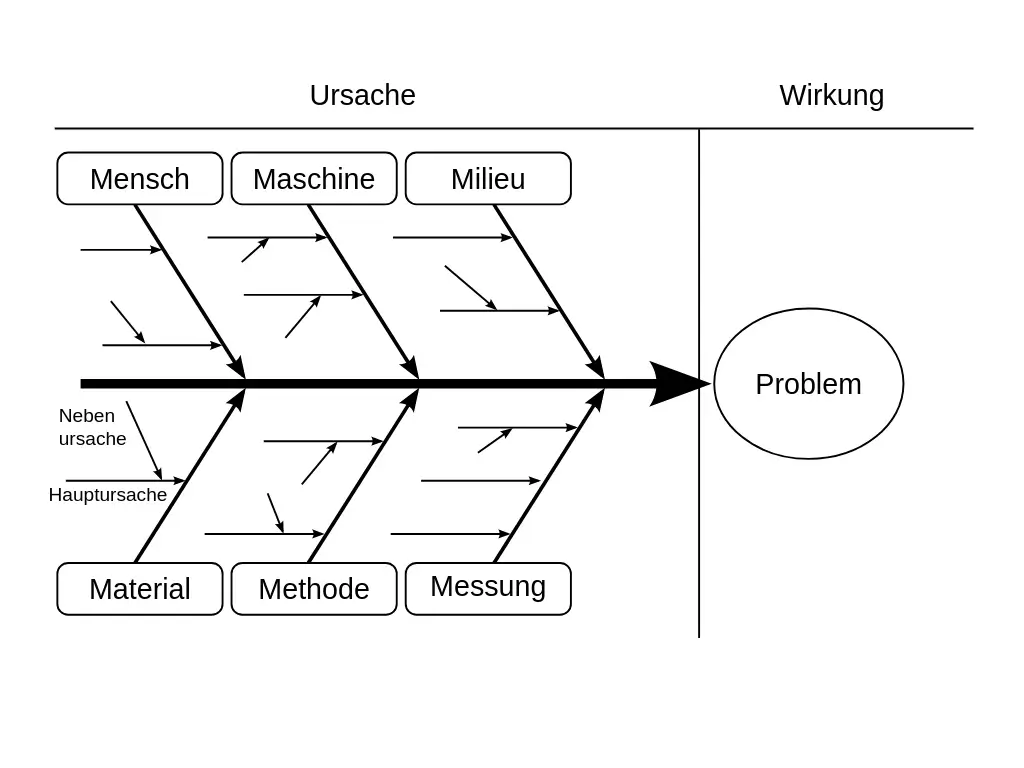
(Fischgräten- oder Ursache-Wirkungs-Diagramm)
Das Ishikawa-Diagramm hilft Unternehmen dabei, systematisch die Hauptursachen von Problemen zu identifizieren. Es visualisiert potenzielle Einflussfaktoren auf ein Problem, indem es diese in verschiedene Kategorien wie Mensch, Maschine, Material, Methode, Messung und Umgebung unterteilt. Dadurch lassen sich Korrelationen zwischen Fehlerquellen und deren Auswirkungen besser verstehen. Diese Methode eignet sich besonders für Teams, die gemeinsam Ursachenanalysen durchführen und nachhaltige Lösungen erarbeiten möchten.
Typische Ursachenbereiche:
- Mensch
- Maschine
- Material
- Methode
- Umgebung
- Messung
Einsatzgebiete:
✔ Qualitätskontrolle und Fehlersuche
✔ Ursachenanalyse bei Produktionsfehlern
✔ Strukturierte Problemlösung in Teams
✔ Kundenreklamationsmanagement
Grenzen:
✘ Zeigt nur potenzielle Ursachen, aber keine Priorisierung
✘ Nicht geeignet für schnelle Entscheidungen oder Notfallmaßnahmen
✘ Erfordert Erfahrung, um richtige Ursachen zu identifizieren
Warum wird das Ishikawa-Diagramm genutzt?
- Einfache und übersichtliche Fehleranalyse.
- Unterstützt strukturierte Problemlösung.
5. 5S-Methode – Ordnung und Effizienz am Arbeitsplatz
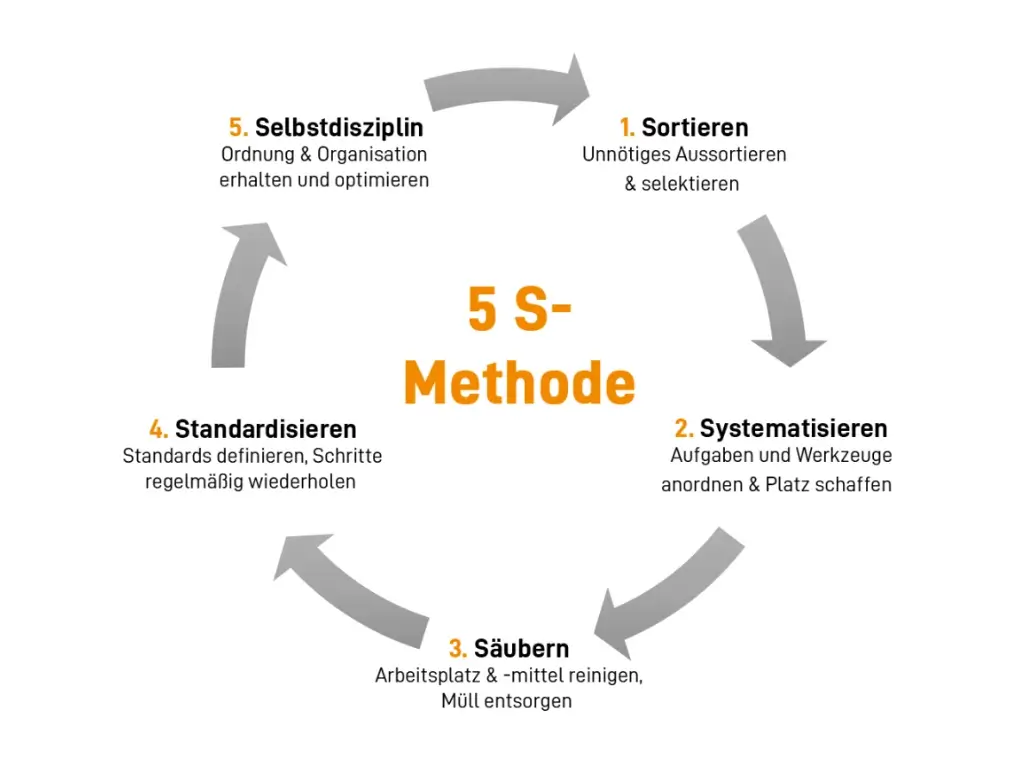
Die 5S-Methode stammt aus Japan und wurde ursprünglich im Toyota-Produktionssystem entwickelt. Ziel ist es, Arbeitsplätze effizient zu organisieren und eine saubere, geordnete Umgebung zu schaffen. Die fünf „S“ stehen für Seiri (Sortieren), Seiton (Systematisieren), Seiso (Säubern), Seiketsu (Standardisieren) und Shitsuke (Selbstdisziplin). Unternehmen, die 5S konsequent umsetzen, profitieren von höherer Produktivität, weniger Verschwendung und gesteigerter Arbeitssicherheit.
Die 5 Schritte von 5S:
- Seiri (Sortieren): Unnötiges entfernen.
- Seiton (Systematisieren): Alles sinnvoll anordnen.
- Seiso (Säubern): Arbeitsplatz sauber halten.
- Seiketsu (Standardisieren): Einheitliche Abläufe schaffen.
- Shitsuke (Selbstdisziplin): Nachhaltige Umsetzung sicherstellen.
Einsatzgebiete:
✔ Arbeitsplatzorganisation in der Produktion
✔ Effizienzsteigerung in Büros und Lagern
✔ Sicherheitsverbesserung in Werkstätten
✔ Lean Management zur Vermeidung von Verschwendung
Grenzen:
✘ Erfordert disziplinierte Umsetzung durch alle Mitarbeiter
✘ Kann ohne nachhaltige Kontrolle wieder in alte Muster zurückfallen
✘ Funktioniert nicht gut in stark kreativen oder dynamischen Umgebungen
Warum wird 5S genutzt?
- Erhöht die Produktivität und Arbeitssicherheit.
- Spart Zeit und Kosten durch effiziente Abläufe.
6. 8D-Report – Strukturierte Problemlösung
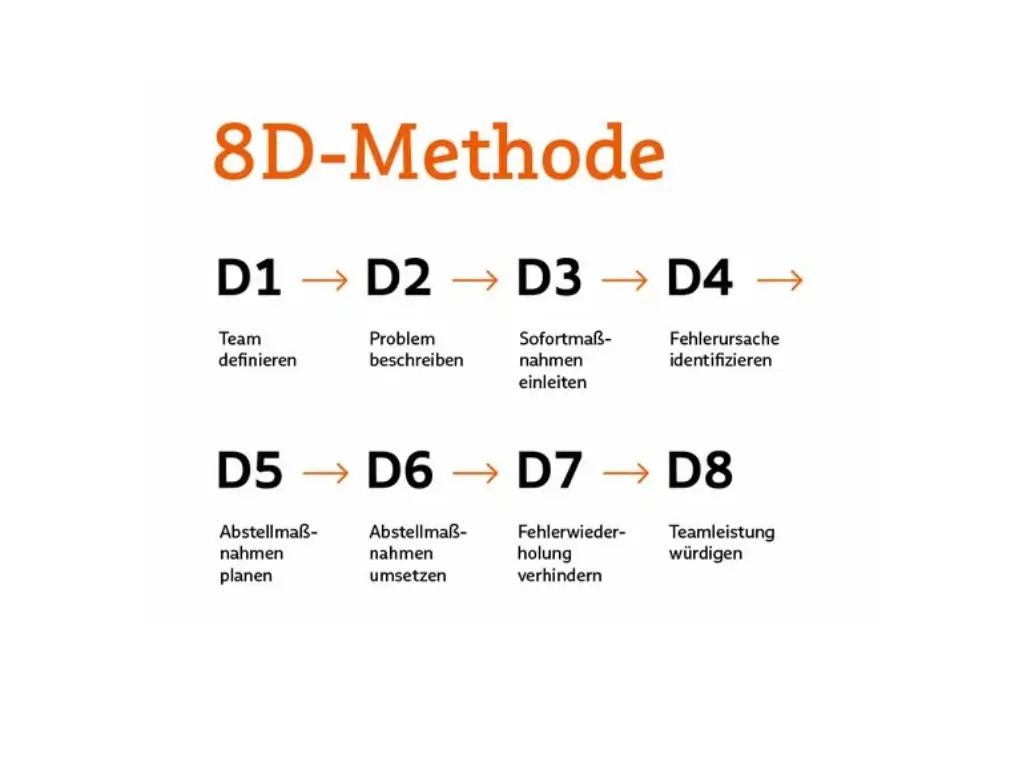
Der 8D-Report (8D steht für „8 Disziplinen“) ist eine strukturierte Methode zur systematischen Problemlösung. Sie wurde ursprünglich von der Automobilindustrie entwickelt, wird aber heute in vielen Branchen eingesetzt. Das Ziel eines 8D-Reports ist es, Fehler nachhaltig zu analysieren und zu beseitigen, um deren Wiederholung zu verhindern. Der Bericht dokumentiert den gesamten Problemlösungsprozess und sorgt für Transparenz gegenüber Kunden, Lieferanten und internen Teams.
Die 8 Schritte des 8D-Reports:
Der 8D-Report ist eine bewährte Methode zur strukturierten und nachhaltigen Problemlösung, insbesondere bei Qualitätsproblemen. Er dient dazu, Fehler systematisch zu analysieren, sofortige Maßnahmen zur Schadensbegrenzung einzuleiten und langfristige Lösungen zu entwickeln, um deren Wiederholung zu verhindern. Der 8D-Prozess umfasst acht Disziplinen (D1–D8), die eine umfassende Problembewältigung gewährleisten.
Die 8 Disziplinen des 8D-Reports im Detail
D1: Zusammenstellen eines Teams für die Problemlösung
Das Team sollte aus Experten mit ausreichender Prozess- und Produktkenntnis bestehen. Die Mitglieder müssen bereit sein, aktiv an der Problemlösung mitzuwirken und über die notwendigen Fähigkeiten verfügen, um die Ursachen zu analysieren, Korrekturmaßnahmen einzuleiten und deren Wirksamkeit zu überwachen. Eine interdisziplinäre Zusammensetzung sorgt für verschiedene Blickwinkel und eine fundierte Lösungsentwicklung.
D2: Problembeschreibung
Eine klare und präzise Definition des Problems ist essenziell. Der Fehler muss möglichst genau beschrieben und quantifiziert werden, um den Kern des Problems herauszuarbeiten. Dazu können Methoden wie 5W1H (Wer, Was, Wann, Wo, Warum, Wie) oder der Problem-Solving-Worksheet eingesetzt werden, um eine vollständige Analyse der Situation zu gewährleisten.
D3: Sofortmaßnahmen festlegen
Sofortmaßnahmen (Corrections) sollen verhindern, dass sich das Problem weiter ausbreitet, bis eine dauerhafte Lösung implementiert ist. Beispiele für Sofortmaßnahmen sind Sortierprüfungen, 100 %-Prüfungen fehlerverdächtigen Materials oder das vorübergehende Anhalten von Prozessen. Diese Maßnahmen dienen ausschließlich der Schadensbegrenzung und sind keine dauerhafte Lösung.
D4: Grundursache(n) identifizieren
In dieser Phase wird die tatsächliche Ursache des Problems ermittelt, um sicherzustellen, dass ähnliche Fehler nicht erneut auftreten.
Hierzu werden häufig folgende Methoden verwendet:
- 5-Why-Methode – Durch fünf aufeinanderfolgende “Warum?”-Fragen wird die eigentliche Ursache herausgearbeitet.
- Ishikawa-Diagramm (Fischgräten-Diagramm) – Systematische Analyse von möglichen Einflussfaktoren wie Mensch, Material, Methode, Maschine, Messung und Umgebung.
- Durchschlüpfpunktanalyse – Untersucht, warum der Fehler nicht vorher entdeckt wurde.
- FMEA (Fehlermöglichkeits- und Einflussanalyse) – Bewertet und minimiert Risiken im Prozess.
Eine nachhaltige Problemanalyse sollte neben der technischen Ursache auch organisatorische Faktorenberücksichtigen, um ähnliche Fehler langfristig zu verhindern.
D5: Planen von Abstellmaßnahmen
Nachdem die Grundursache ermittelt wurde, müssen geeignete Maßnahmen zur dauerhaften Fehlerbeseitigung (Corrective Actions) entwickelt werden. Die ausgewählten Lösungen sollten durch Tests und Experimente validiert werden, um sicherzustellen, dass sie den Fehler effektiv und effizient beheben, ohne unerwünschte Nebenwirkungen zu verursachen. Ein erfolgreiches Maßnahmenmanagement sorgt dafür, dass das Problem nicht erneut auftritt.
D6: Einführen der Abstellmaßnahmen
Die entwickelten Maßnahmen werden nun in den regulären Betrieb integriert. Änderungen können sich auf Prozessparameter, Spezifikationen, Prüfmethoden oder auch die Mitarbeiterqualifikation auswirken. Sobald die Abstellmaßnahmen erfolgreich umgesetzt wurden, können die vorher definierten Sofortmaßnahmen aufgehobenwerden.
Wichtig: In der Automobilindustrie gilt, dass nur prozessverbessernde Maßnahmen als Abstellmaßnahmen akzeptiert werden. Personelle Maßnahmen (z. B. Schulungen, Ermahnungen) gelten nicht als nachhaltig und werden nicht als Lösung anerkannt.
D7: Fehlerwiederholung verhindern
Um sicherzustellen, dass der Fehler dauerhaft beseitigt ist, müssen Mechanismen zur Überwachung der Wirksamkeitimplementiert werden.
Typische Maßnahmen sind:
- Erhöhte Prüfschärfe über einen bestimmten Zeitraum
- Anpassung der Qualitätsmanagementprozesse
- Überarbeitung der FMEA, um neue Erkenntnisse in die Produkt- oder Prozessentwicklung einfließen zu lassen
In der Automobil- und Luftfahrtindustrie ist es erforderlich, dass erkannte Risiken in der Entwicklung und Produktion systematisch bewertet und minimiert werden.
D8: Würdigen der Teamleistung
Ein erfolgreich abgeschlossenes 8D-Verfahren sollte nicht nur dokumentiert, sondern auch analysiert werden. Die Teammitglieder sollten für ihren Einsatz anerkannt werden, und die gewonnenen Erkenntnisse sollten genutzt werden, um das Unternehmen insgesamt zu verbessern. Erfahrungen und Best Practices sollten in das kontinuierliche Verbesserungsprogramm (KVP) integriert werden, um zukünftige Fehler zu vermeiden.
Einsatzgebiete:
✔ Reklamationsmanagement und Kundenfeedback
✔ Qualitätsabweichungen in der Produktion beheben
✔ Dokumentation und Nachverfolgung von Fehlerursachen
✔ Lieferantenmanagement und Verbesserung der Zusammenarbeit
Grenzen:
✘ Kann für kleinere Probleme zu komplex sein
✘ Erfordert detaillierte Dokumentation, was aufwendig sein kann
✘ Funktioniert weniger gut für sofortige, schnelle Lösungen
Warum wird der 8D-Report genutzt?
- Sorgt für eine nachhaltige Fehlerbehebung.
- Häufig genutzt im Reklamationsmanagement.
7. Lean Management – Verschwendung eliminieren
Lean Management ist eine philosophische und methodische Herangehensweise, die darauf abzielt, Verschwendung (Muda) zu minimieren und Prozesse effizienter zu gestalten. Der Ansatz stammt aus der Toyota-Produktionsmethode und wird heute in vielen Branchen angewendet. Ziel von Lean ist es, maximalen Wert für den Kunden zu schaffen, indem alle unnötigen Prozesse und Ressourcen eliminiert werden.
Die 5 Prinzipien des Lean Managements:
- Wert definieren: Identifikation des Kundennutzens und Fokussierung auf wertschöpfende Tätigkeiten.
- Wertstrom identifizieren: Analyse der Prozesse, um Verschwendung sichtbar zu machen.
- Fluss-Prinzip: Sicherstellen, dass Prozesse ohne Unterbrechungen ablaufen.
- Pull-Prinzip: Produktion erfolgt basierend auf der tatsächlichen Nachfrage, nicht auf Prognosen.
- Kontinuierliche Verbesserung (Kaizen): Fortlaufende Optimierung von Prozessen.
Die 7 Arten der Verschwendung (Muda):
- Überproduktion – Herstellung von mehr als benötigt wird.
- Wartezeiten – Verzögerungen durch ineffiziente Abläufe.
- Transport – Unnötige Wege für Materialien und Produkte.
- Überflüssige Prozesse – Schritte, die keinen Mehrwert schaffen.
- Bestände – Zu hohe Lagerbestände binden Kapital.
- Bewegung – Unnötige körperliche Bewegungen und Wege.
- Fehler/Nacharbeit – Mängel, die zusätzliche Arbeit erfordern.
Einsatzgebiete:
✔ Produktionsoptimierung (z. B. Toyota-Produktionssystem)
✔ Reduzierung von Durchlaufzeiten und Kosten
✔ Verbesserung der Effizienz in Dienstleistungen und Verwaltung
✔ Logistik und Lagerhaltung
Grenzen:
✘ Kann bei extremer Kosteneinsparung zu Qualitätseinbußen führen
✘ Erfordert kontinuierliche Anpassung, da sich Prozesse verändern
✘ Nicht immer geeignet für stark regulierte oder standardisierte Prozesse
Warum wird Lean Management genutzt?
- Erhöht die Effizienz und Kostenersparnis.
- Verbessert die Produktivität in Produktion und Verwaltung.
Welche Methode ist die beste?
Es gibt keine universell beste Qualitätsmethode – jede hat ihren spezifischen Anwendungsbereich. Unternehmen kombinieren häufig mehrere Methoden, um eine optimale Qualitätssicherung zu gewährleisten.
Unser Tipp:
- Nutzen Sie PDCA für kontinuierliche Verbesserungen.
- Verwenden Sie FMEA zur präventiven Fehlervermeidung.
- Setzen Sie auf Lean und 5S, um Prozesse zu verschlanken.
- Six Sigma eignet sich für datenbasierte Prozessoptimierung.
Möchten Sie Ihr Qualitätsmanagement verbessern?
Qualitätsmethoden wie Lean Management, 8D-Report und Six Sigma helfen Unternehmen, Prozesse zu optimieren und Fehler zu vermeiden. Erfahren Sie mehr über die Vorteile einer ISO 9001-Zertifizierung in unserem Blogartikel!
Besuchen Sie unseren Etsy-Shop für Vorlagen und Tools, die Sie bei der Implementierung unterstützen!